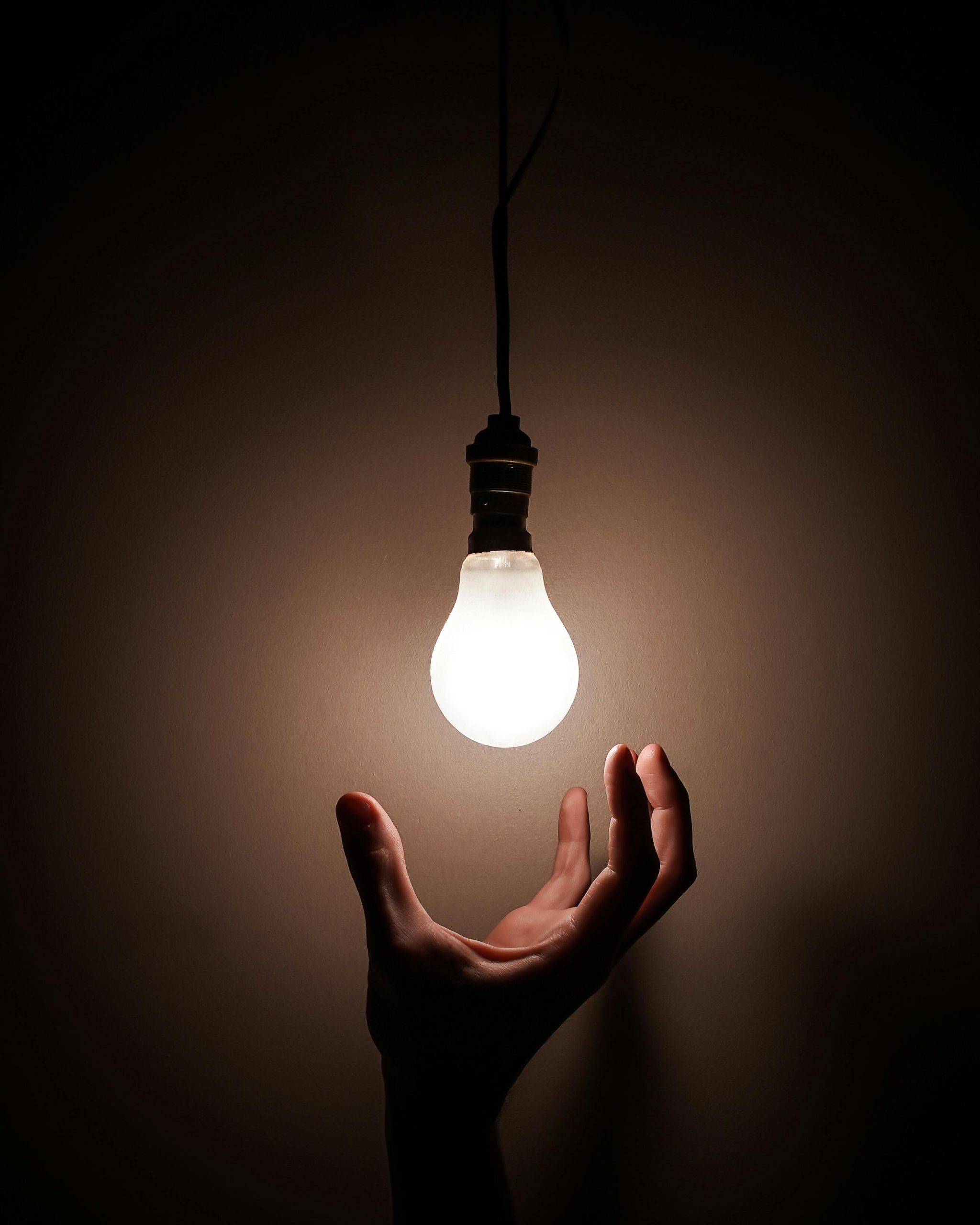
Ten Tips For Saving Energy
Power-saving/ Energy-saving methods are the ways and ideas through which it is possible to reduce the burden of delivering power at the load end or reducing loads as much as possible. With proper power-saving techniques, industries can save millions of dollars spent on wasted energy, and utility companies can meet their power demands and save the same energy cost.
For example, turning off unnecessary lights and machinery when not in use and replacing an old high-power motor with a lower-power but efficient one is a great way to reduce costs. There are many industries that use old motors, which need to be replaced. Suppose a motor with an efficiency of 83% has an electric cost per year of N5,472,600. When replaced with a motor having a high efficiency of 87.5%, will consume electric power worth 5,209,000 and annual savings of N263,650 can be achieved.
Power saving or conserving energy has become important nowadays due to the following reasons:
As the power requirement is increasing day-by-day due to the advancement in technology, the requirement for fossil fuels has also increased. An increase in the consumption of fossil fuels is causing pollution within the environment.
Also, at each level be it commercial, industrial, or residential, irresponsible attitude and unnecessary wastage of electricity is reflected as high costs in our utility bills.
Losses in equipment such as heating due to motor overload, oversized cables and motors, dim old lighting, and less efficient machinery also result in wasteful energy consumption.
So to reduce pollution, mitigate losses, and reduce the cost of electricity, power-saving has become essential.
Here are Ten Tips for Efficient and Effective Energy-Saving.
1. Energy Policy:
An energy policy is a document or set of regulations that include strategies and steps to be taken for energy saving. There are several standards based on which energy policies are made.
For example, ISO 50001, a standard made for energy management purposes has the following features:
- Making energy policy for efficient use of energy.
- Setting targets and objectives for policy.
- Data review for better understanding and decision-making of energy use.
- Results measurement.
- Reviewing policy
- Improving policy
2. Energy Audit:
A regular energy audit helps in finding out the power losses due to different equipment, also the areas where most of the power is consumed, and what steps are required to be taken to reduce power consumption without affecting production.
An energy audit consists of the following steps:
Walkthrough Audit: This involves the analysis of overall area major and minor loads, type of work performed there, number of staff, shifts, timings, etc. The results of these audits can be like replacing old CFL lights with LED and reducing the number of switches per luminary etc.
Detailed Audit: This includes data collection, bill comparison, losses due to equipment, replacing old equipment with a new one and its payback period calculation, and what major steps need to be taken by a facility for power saving which might include educating their workers about energy-saving steps and offering incentives to employees who show responsibility towards them.
3. Renewable Energy:
The use of renewable energy is becoming common nowadays as it is a free source of energy and has almost negligible carbon emissions. Renewable energy includes the use of wind energy, solar energy, biomass energy, and many more. These energies are utilized for supplying load through the combination of power system equipment besides power electronic devices. The use of renewable energy in industrial facilities can also be a source of cost-saving and reducing demand on the utility company. For example: On an industrial scale installing solar panels and shifting the lighting load to it can help reduce the burden of power generation greatly.
4. Efficient Lighting:
Electronic Ballast:
The use of electronic ballast in tube lights instead of using an old electromagnet blast can also reduce energy consumption.
LED Lights:
Replacing fluorescent and incandescent with low-power LED lights is a fine approach to saving energy. For example: on replacing a 40-watt and 500-lumens incandescent bulb with a 7-watt LED bulb providing the same lumens (brightness), then about 33 watts (40 minus 7) can be saved per luminaire.
Lighting Control through Sensors:
Sensors-based light in washrooms and other areas can save a lot of energy. For example, an office has a working hour of about 10 hours and washroom lights remain on during the complete hour. Instead of turning on the light throughout the office hour, ultraviolet sensor-based light can be used in the washroom which turns on only when it senses any physical thing moving around it, this will reduce the waste of energy.
5. Power Factor:
The power factor shows the ratio of the amount of power utilized for doing useful work from the power that is supplied. Most of the motors present in industries are induction motors. The power supplied to an induction motor is used for two purpose
Firstly, to do some useful work usually rotating work known as active power.
Secondly, to maintain the magnetic field known as reactive power.
It is preferred that reactive power should be minimal. An increase in reactive power reduces the power factor and low-power factors cause penalties on the industry.
For example, two industries are supplied by a grid having the following data:
DATA INDUSTRY A INDUSTRY B
Power utilized 1 MW 1 MW
Power factor (P.F) 0.5 0.8
Power required (MW/P.F) 2 MVA 1.25 MVA
The given data shows that both industries may have the same amount of motors utilizing 1 MW for doing useful work but due to the difference in power factor the power supplied by the grid changes. Industry A will have to pay a high bill as the grid has to supply more power.
So to compensate for reactive power requirement, synchronous condensers, STATCOM, and capacitor banks are used.
6. Motor:
Motor Rewinding:
Due to overloading, voltage fluctuation, and insulation damage, motor winding temperature increases and starts to get damaged. The rise in temperature leads to increased losses. It is said that motor life gets halved at every 10-degree rise in its temperature.
For this purpose, we send motors for rewinding. But if rewinding is performed with a lack of care and precautions then every rewinding could cause a 1% decrease in efficiency which ultimately results in increasing the cost of electricity.
The following points should be under consideration while deciding on motor rewinding:
If the motor fails 3 times in its life then it should be replaced with a more efficient motor instead of rewinding it.
Capacity rated current, winding design and no-load current variation should be known.
No harm or damage should be done to the core or insulation.
Make sure that the no-load current does not increase after rewinding.
Rewinding should be performed in a dust-free environment.
Motor Staggering:
At the time when the motor starts, it consumes almost three times as much power as its rated power. So for industries that have numerous motors, it is recommended that each motor should be started one by one after some delay. This will reduce the overall burden on the electricity generation end thus reducing the fuel cost.
For example:
An industry consists of three motors each of 10 KW and having a starting power of 30 KW for a few seconds. If all the motors are started in one go, then the surge of 90KW will appear at the generation end. Instead, if the motors are started one at a time then the surge will be much less.
Control Systems in Motor:
Motors can be used at high efficiency using power electronics devices. For example:
Problem
At the time of starting, the motor draws a larger amount of current than the rated current. Eventually the requirement of power increases.
Solution
A 'soft starter' reduces the starting current for high HP motors. For low HP motors, star-delta starters and DOL (Direct On-Line) starters can also be used.
Problem
A motor works better at its rated speed when it is provided the full load. As the load decreases the motor will provide the remaining power to cater to the losses, resulting in less efficiency.
Solution
A 'Variable Speed Drive (VSD)' proportionally changes speed as the load varies.
7. Housekeeping and Maintenance Plan:
Proper scheduled maintenance and monitoring of loads in industries could increase the life span of equipment and also help in controlling losses or failure.
For example:
Lights can get dusted easily and get dim. Scheduled cleaning of lights results in proper brightness and increases its life span.
Voltage imbalance can cause the failure of the motor. Monitoring voltage imbalance and mitigating it can save the motor from large damages
As motors run continuously in certain industries, this can result in increased motor temperature. More overexposure to a rough environment also leads to body damage and insulation failures. A proper maintenance schedule for regular maintenance, inspection, and cleaning is a good option for motor protection from environmental adverse effects.
8. Cogeneration/Combine Cycle:
Cogeneration means using exhaust heat for heating or cooling. Many industries out there have a heating or cooling process so instead of wasting the heat of exhaust they can reuse it to generate electricity or provide heating somewhere else. Gas turbine and Gas engine generators also produce exhaust heat having high temperatures. This heat energy can be utilized instead of being released to the environment. The hot exhaust gases can be directed towards the HRSG (Heat recovery steam generator) which then produces steam that can be utilized for electricity generation using steam turbines or any other heating purpose. This is known as the combined cycle. These combined cycle plants are highly efficient and greatly reduce energy losses saving fuel costs.
9. Heating and Cooling /HVAC:
HVAC (Heating Ventilation and Air conditioning) are used in almost all process industries, commercial buildings, and homes. The following steps can be taken to make efficient use of HVAC.
Clean air vents can save up to 25% of energy which could be utilized while pumping air into space.
The properly sealed room helps the AC or heater compressor to use less power.
Shaded windows can be used for the prevention of heatwaves where cooling is required. This reduces the electricity required to maintain temperature by air conditioners.
10. Load Management:
Due to changes in shifts, variations in weather, and different production times, demand never remains the same. Such variation in load causes an increase in the number of generators which proportionally increases the maintenance and control system requirement and thus cost increases.
Proper load management like reducing unnecessary loads like lights, motors, and economic dispatch of power improves our energy savings in such cases.
Another method that can be employed to reduce peaks is using control systems or a 'Smart Grid', a central unit that carries the supply from certain loads and automatically cuts off or sets off an alarm whenever it reaches a certain peak.
Peak shaving can also be done through a distributed generation supplied by both grid and self-generation. Here, self-generation means that having a gas, diesel generator, or UPS (uninterruptable power supply) present at your facility can be used as a backup supply or for peak demand supply.